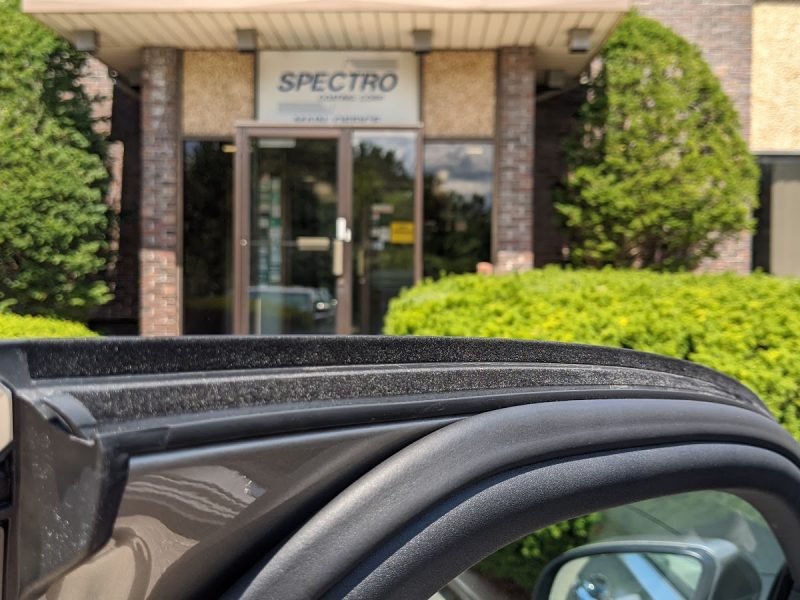
Flocked window seals have been around for over 50 years. Flocking provides a unique high value solution for this application. Many automotive companies have tried to remove or replace it with little success. The performance and durability of flocking for this application is unmatched.
Flocking is the application of short cut precision fibers to a surface using an adhesive. The adhesive is applied to the surface precision fibers are electrostatically coated and are perpendicular to the surface. This results in a soft velvet feel. The fibers primarily used for the flocking of rubber profiles are polyester and nylon.
The flocking of window seals provides unique advantages. It allows for a good seal against a moving surface. As windows are moved up and down, the flock fibers shape around the widow. The fibers act as a cushion and compensate for movement of the glass. The cushioning effect also helps reduce any noise, vibration, and hissing sounds.
By flocking the EPMD or TPU, you are also reducing the coefficient of friction. Without the flock fibers the EPMD or TPU profile by itself would have a high coefficient of friction leading to added burden of the powered mechanisms when moving the window. In hot weather, the rubber will stick to the glass resulting in failure of the powered window. The rubber could also transfer over to the glass over time.
The flocked fibers do not hold any of the debris from the outdoors. The fibers will let go of any sand or particles that could imbed in the rubber profile which would result in scratches in the glass. It also helps prevent any debris from getting in the door and into the mechanism. The flock fibers act as a brush when the window is moving down. The flocking holds up to the elements, and can help clean off rain, condensation, or snow when the window is lowered and raised.
The flocking process also brings an aesthetic appeal over the plain rubber. It will not come off or stick to the glass. It has a soft velvet feel, and a high-performance value.
Traditionally flock has been applied using adhesive and flocking chambers in the flocking process. This leads to large production lines that must include adhesive application equipment and flocking chambers. Flocking is traditionally applied in conditioned rooms. The process of applying short cut fibers leads to additional housekeeping and environmental requirements. The adhesives used to bond to EPMD or TPU are typically solvent based. All these additional processing, housekeeping, and environmental requirements add to additional indirect costs when manufacturing the rubber profiles.
Flock tape brings a cleaner and simpler process. The flock tape is made in wide width at the flock coating plant designed to handle these materials. The film is then slit and spooled to the desired length and width. The slit spools are then shipped to the window sealing plant. This removes all the added burden of the traditional flocking process at the window sealing manufacturing plant. It also reduces the footprint, labor, and maintenance costs of the rubber profile extrusion line, as the traditional flock equipment previously required, is no longer needed.
Now the flock tape is introduced at the same time as the rubber profile is extruded through the die. The tape melts to the rubber by passing through the same die that shapes the profile. The rubber is cooled and cut to the desired length and the flock tape is permanently melted to the rubber. The fibers are only exposed to the high heat of the die for less than a second, preventing the fibers from melting or crushing due to the short exposure time.
Flock tape may not be the ideal situation for intricate turns and shapes, but automotive engineers have learned to design around these issues.
Our special proprietary flocking finish also helps reduce any squeaking noises in damp conditions between the flocked profile and the window. We also have the ability to apply specified topical coating to the flock tape,including Resilon and Klubertop, in a cost effective process.

Our division, American Flock Tape, provides the slit spools of flock tape used in the window sealing systems. We have the capacity to slit 50,0000,000 meters of tape, and will double this capacity in 2021. Since, we have our own flocking in house, we have the ability to also manufacture specific colors of flock tape.
Today, Spectro Coating Corp. houses the world’s largest flocking operation under one roof. Our roots in flocking go back over 75 years. Our 180,000 square foot facility produces much of the world’s finest and most unique suede, velvet, and coated products. From commercial furnishings, to drapery and apparel, from automotive, to medical and industrial applications, Spectro Coating Corp. supplies short cut precision flock fiber and coated products worldwide for almost every conceivable use.

We use only water based adhesive systems in our flocking process. Our fibers are pigmented before extrusion, reducing our water processing, and increasing our flock fiber weathering performance. In 2018 we have installed solar panels that provide 1/3 of our electrical usage. By spring of 2021 we will have installed a second solar hot water system which will reduce our heating capacity for our boiler system. We are ISO 2009:2015 and Minority Business Certified.
Our Division, Claremont Flock, provides custom cut and dyed short cut flock fibers for automotive flocking and other flocking applications, paper, filtration, battery pastings, fillers, and many other industries.
Our team works as part of your team. With the most experience in the industry. There is not a challenge we cannot meet.
Please call us for samples and to discuss your needs at 978-534-1800.
